Coastal power plant case study
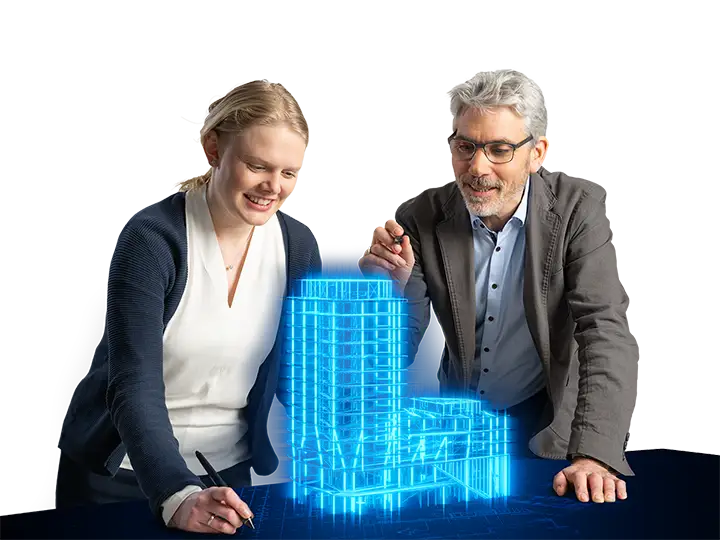
Facts and figures
Testing of the following components:
- Heat accumulator
- E-boiler hall
- Pipe bridge
- Chimneys
- Cooling pit
- Warehouse
- Motor halls
- Workshop hall
- Control center
- Gas transfer station
Climate-friendly heat supply in Kiel
With a total investment volume of around € 290 million, the coastal power plant is the largest investment project in the history of Stadtwerke Kiel. Since 2020, the lighthouse project has saved around 1 million tons of CO² annually. Compared to the coal-based predecessor power plant, emissions will thus be reduced by 70 %!
Combined heat and power generation
For a flexible and sustainable heat supply, Kieler Stadtwerke relies on combined heat and power generation with a thermal efficiency of 46% and an electrical efficiency of 45%. The concept is based on the interaction of gas engines, electrode boilers and heat storage units and enables an immediate response to the demand for electricity and heat: The storage tank is filled when the gas engine CHP plant is producing, but the heat is not needed at that time - or when the electrode boiler is producing heat that is not currently required. The approximately 73,000 district heating customers can be reliably supplied for up to eight hours with the stored hot water.
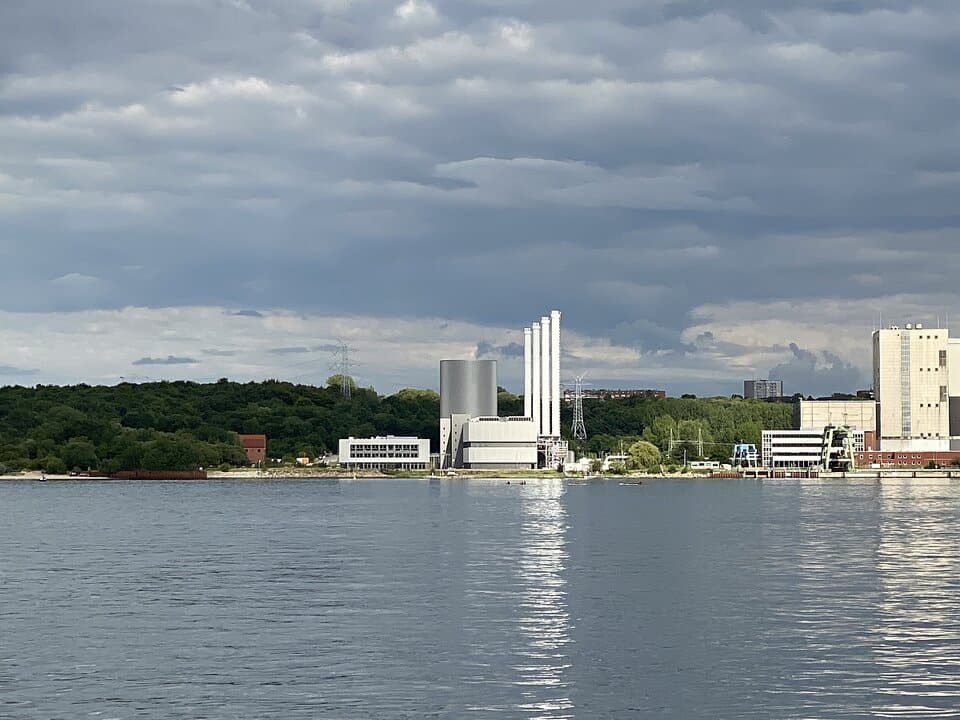
From zero to 191 megawatts in 5 minutes
Whereas the former joint coal-fired power plant took at least four hours to start up, the 20 gas engines take less than five minutes to reach a nominal output of 191 MWh. At the same time, a heat output of 200 MWh can be generated. Each module is designed for several starts per day, so that the power output of the individual engines can be adapted to the current energy demand and fed directly into the district heating network.
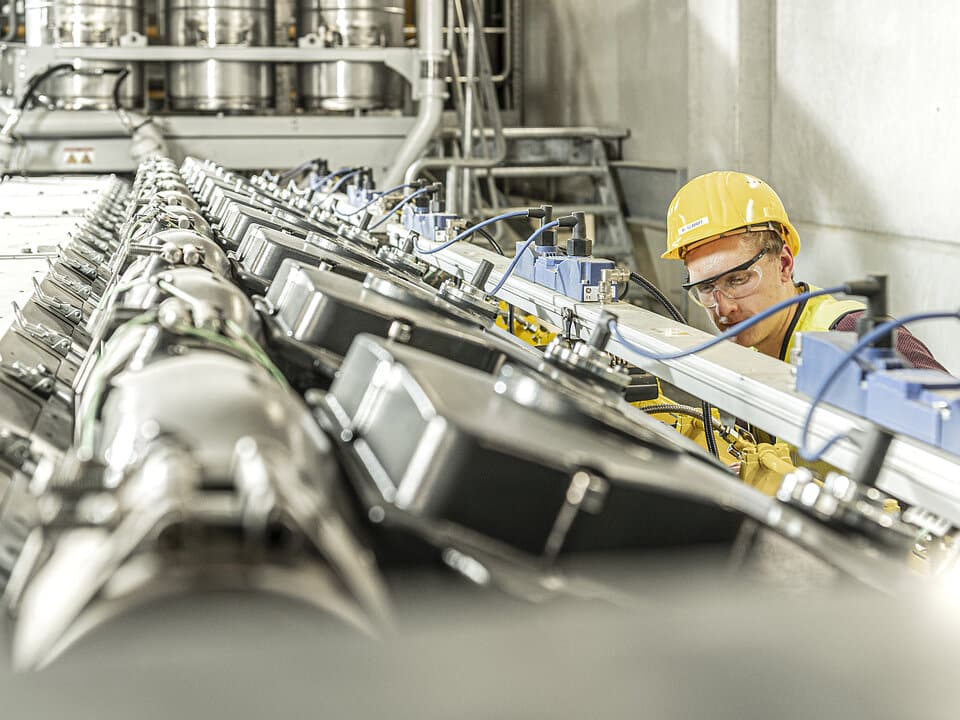
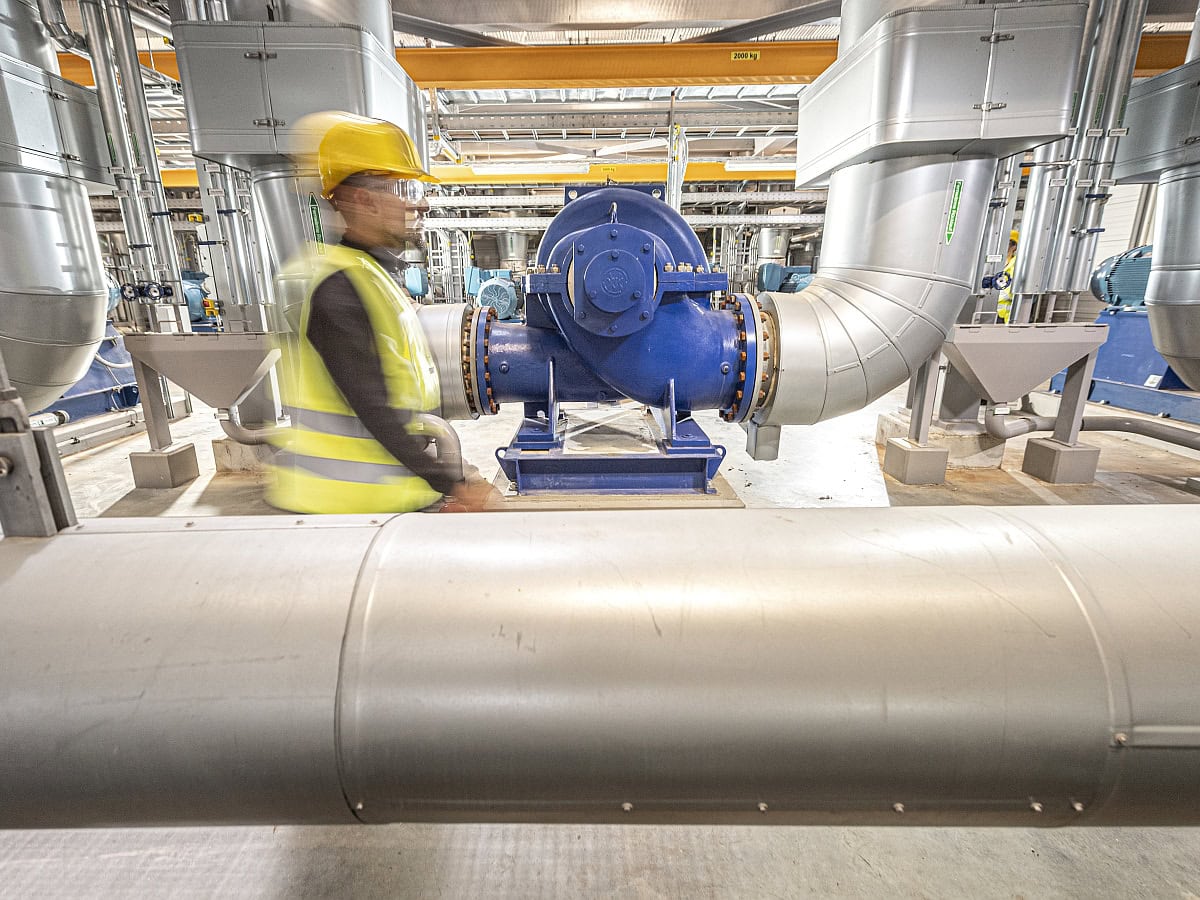
Electrode boiler
It is 6.50 meters high and 3.90 meters wide: the electrode boiler. With 17 electrodes and a total weight of 18,000 kilograms, it achieves an electrical output of 30 MW. Here, the excess supply of electrical (wind/solar) energy is used to heat water with electricity. The heat generated is pumped directly into the heat storage tank, which in turn - in the form of hot water - can be used with a time delay.
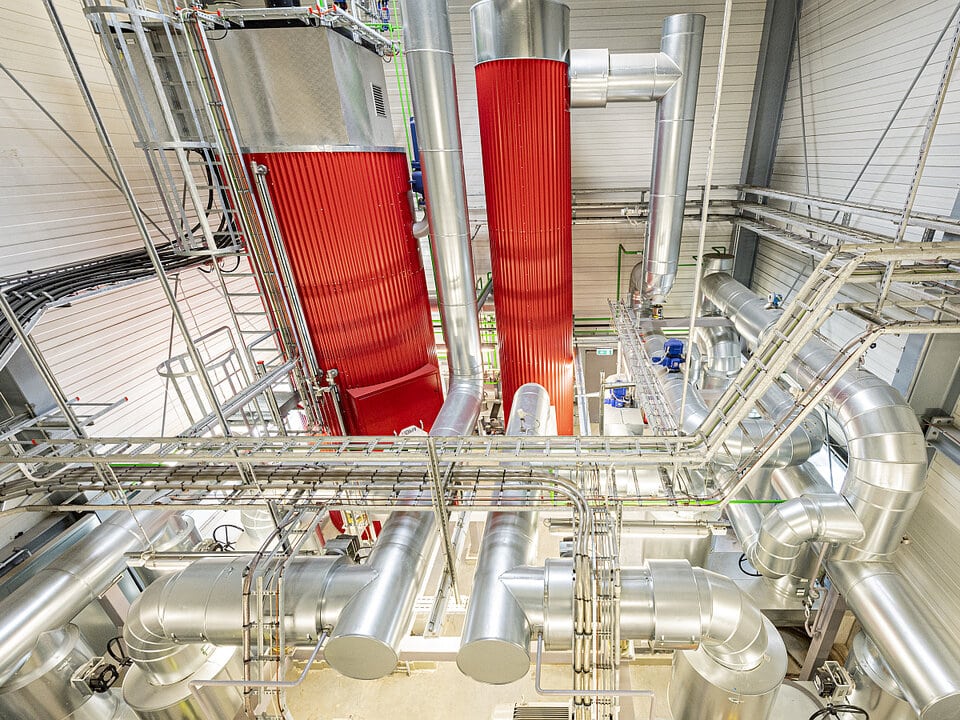
Heat accumulator
The heat storage tank of the coastal power plant is 60 m high, has a diameter of 30 m, a capacity of 42,000 m³ and a guaranteed heat storage capacity of approx. 1,500 MWh. The cylindrical flat-bottomed steel tank stands on 121 bored piles and was built on site using the spiral construction method. The steel construction of the tank consists of thermomechanically rolled fine-grained structural steels S 460 ML suitable for welding. It is designed for an operating overpressure of 190 mbar with a maximum operating temperature of 120 °C for the storage medium water.
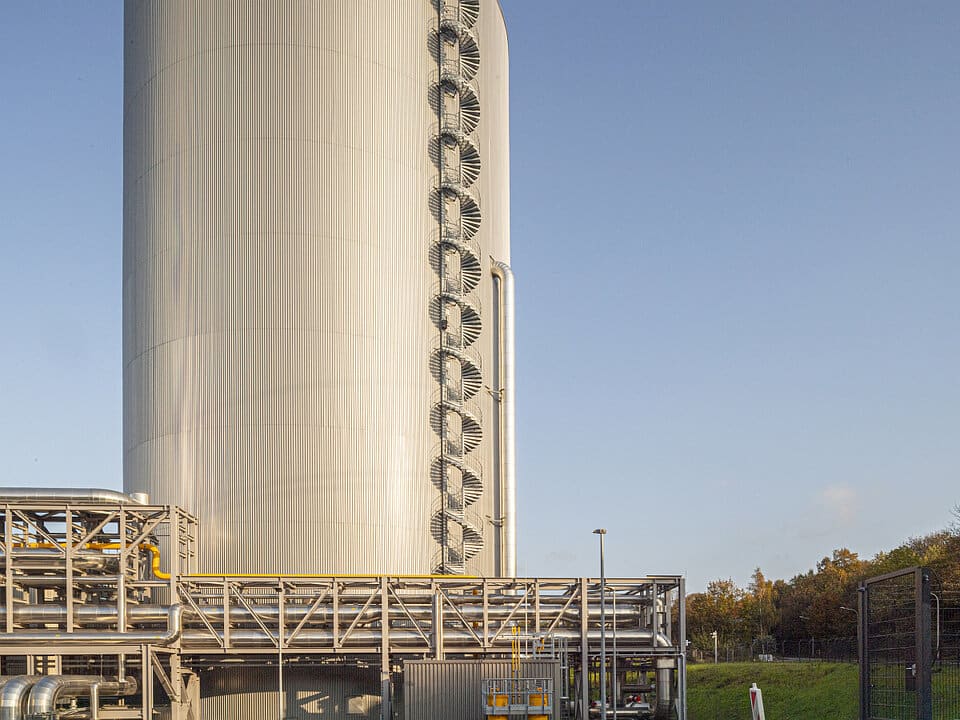
At a glance: Data of the thermal accumulator
- Outer diameter approx. 31 m
- Height with roof and insulation 60 m
- Total volume approx. 42,000 m³
- Useful volume approx. 30,000 m³
- Temperature of hot pendant line 115 °C
- Temperature cold pendant line 60 °C
- Guaranteed heat storage capacity approx. 1,500 MWH
- max. loading and unloading capacity approx. 200 MW
- max. loading and unloading mass flow 3,100 t/h