CHEFS
CULINAR North-East
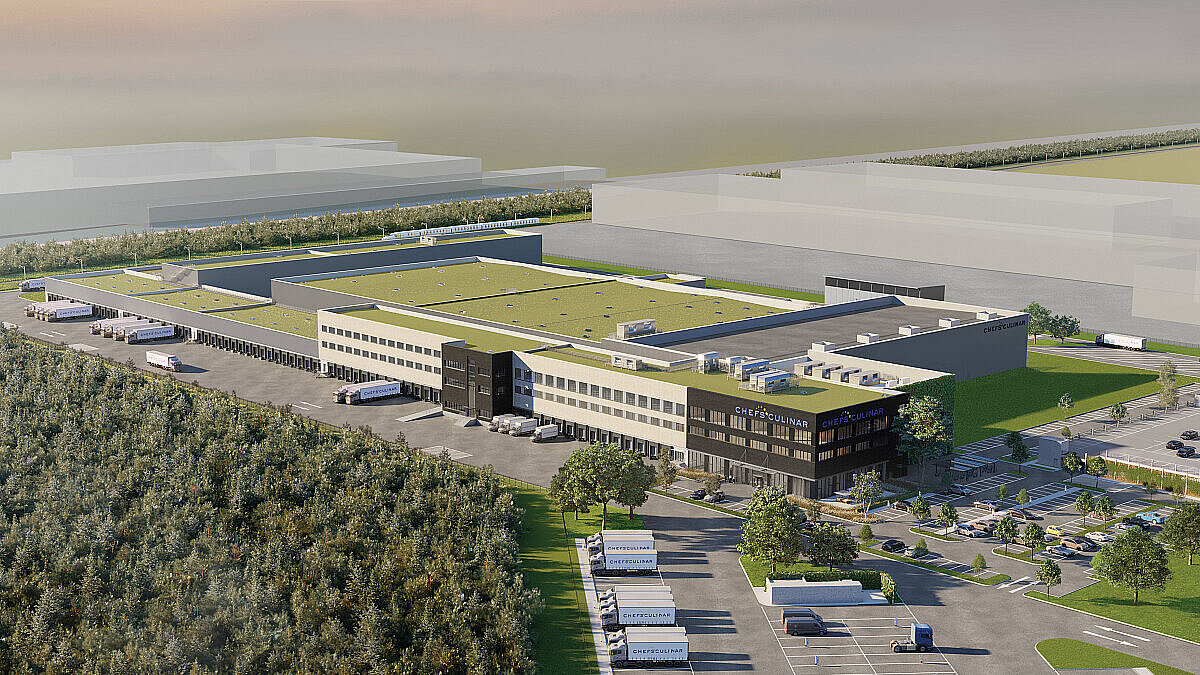
Facts and figures
- Interdisciplinary planning using the BIM method (big-BIM)
- Highest demands in the planning of logistical processes
- Extensive building physics and structural analysis of the structural behavior at different temperature zones (frozen food storage, fresh food storage, production areas)
- Underground sprinkler tanks with a total capacity of around 2,280 m³
- Prefabricated construction with prestressed concrete girders, span 24 m
- Parking garage in composite construction
CHEFS CULINAR wholesale base
The CHEFS CULINAR wholesale chain has a broad base throughout Germany: Around 25,000 articles for the food and non-food sector are stocked at 8 branches and 23 bases. In addition, professional consulting services, seminars and IT solutions are offered to customers in the catering, hotel and communal catering sectors. In 2019-2021, the CHEFS CULINAR North-East wholesale base was established in Ludwigsfelde in the form of a logistics and service center for the greater Brandenburg area.
BIM as 1st choice
Planning with the BIM method pays off, especially for complex buildings such as wholesale warehouses plus production facilities. The building complex at CHEFS CULINAR consists of several sections with different floor structures. The usual specialist areas (electrics, heating, ventilation and water supply) corresponded with the other trades such as fire extinguishing and sprinkler systems, cooling, compressed air, conveyor technology (saturated conveyor), fish and meat cutting (incl. meat pipe conveyor), logistics with automatic small parts warehouse. All information on planning and utilization from the respective specialist models was combined in an overall model.
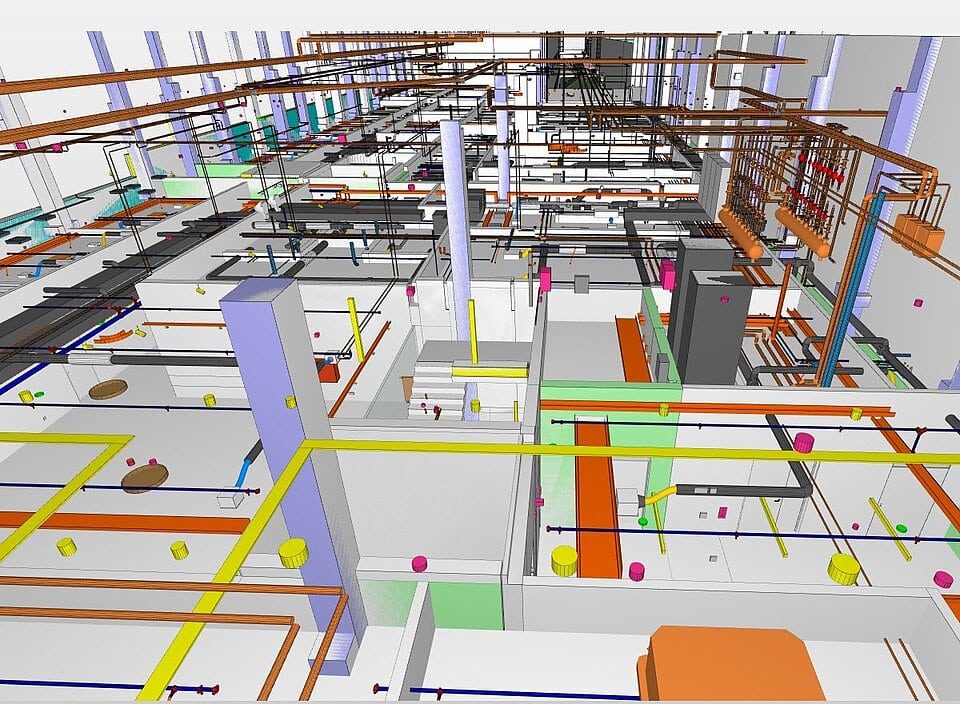
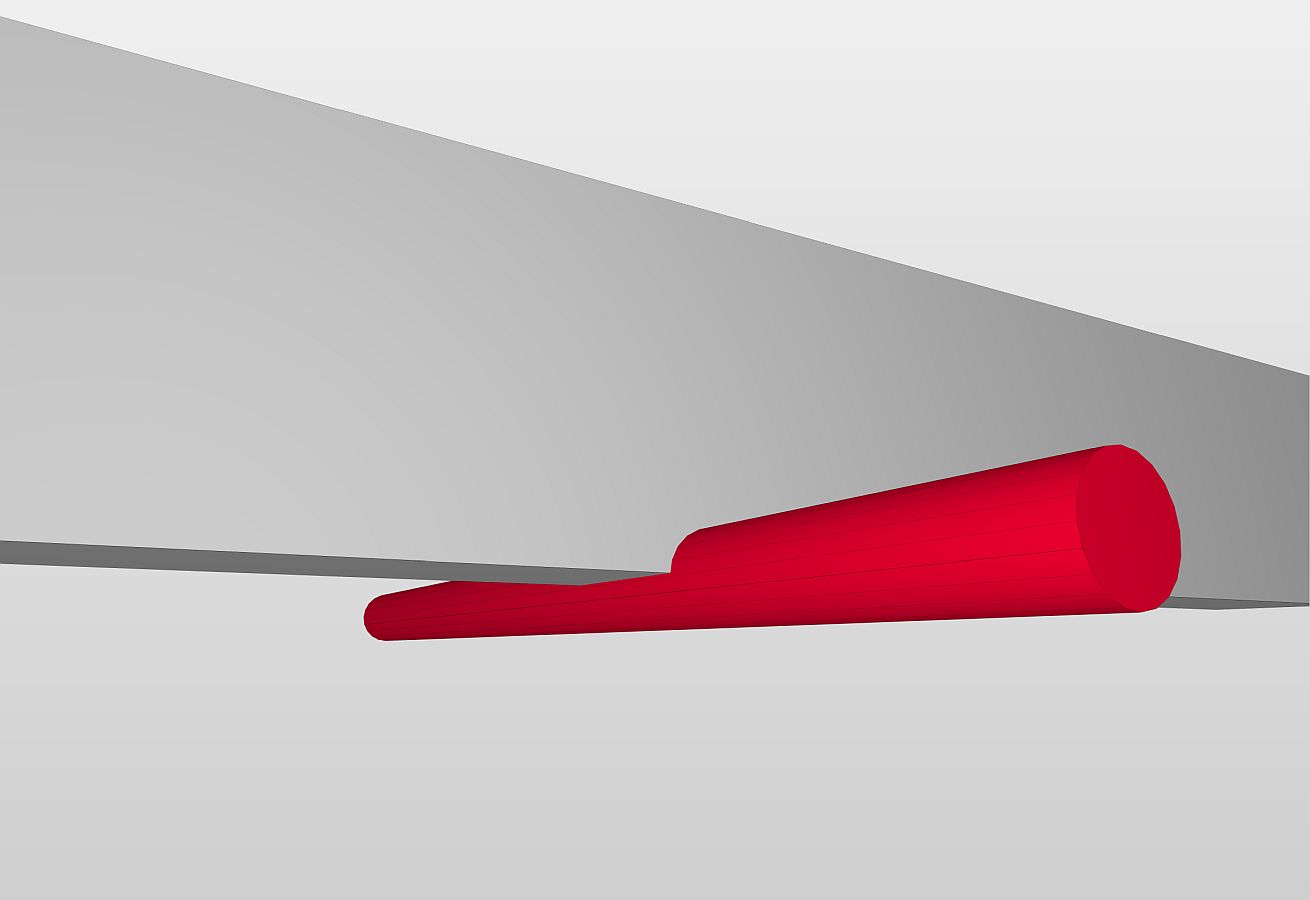
Aspects of overall BIM coordination
Many planners now work with 3D models, which do not necessarily include the use of the BIM method. To ensure that everyone involved in the project had the same level of knowledge to ensure smooth collaboration, we held workshops during the planning phase. They ensured that all relevant information was included in the model. As the client was already using a CAFM (computer-aided facility management) system, it was necessary to record the required information in a LOI (level of information) matrix and integrate it into the client information requirements for commissioning the general contractor.
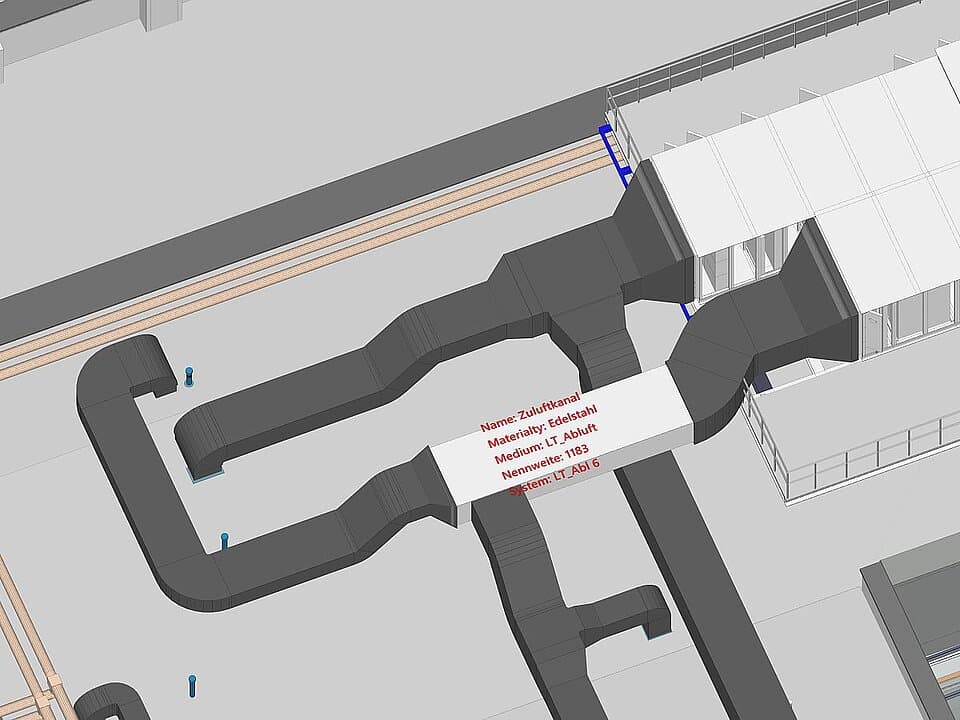
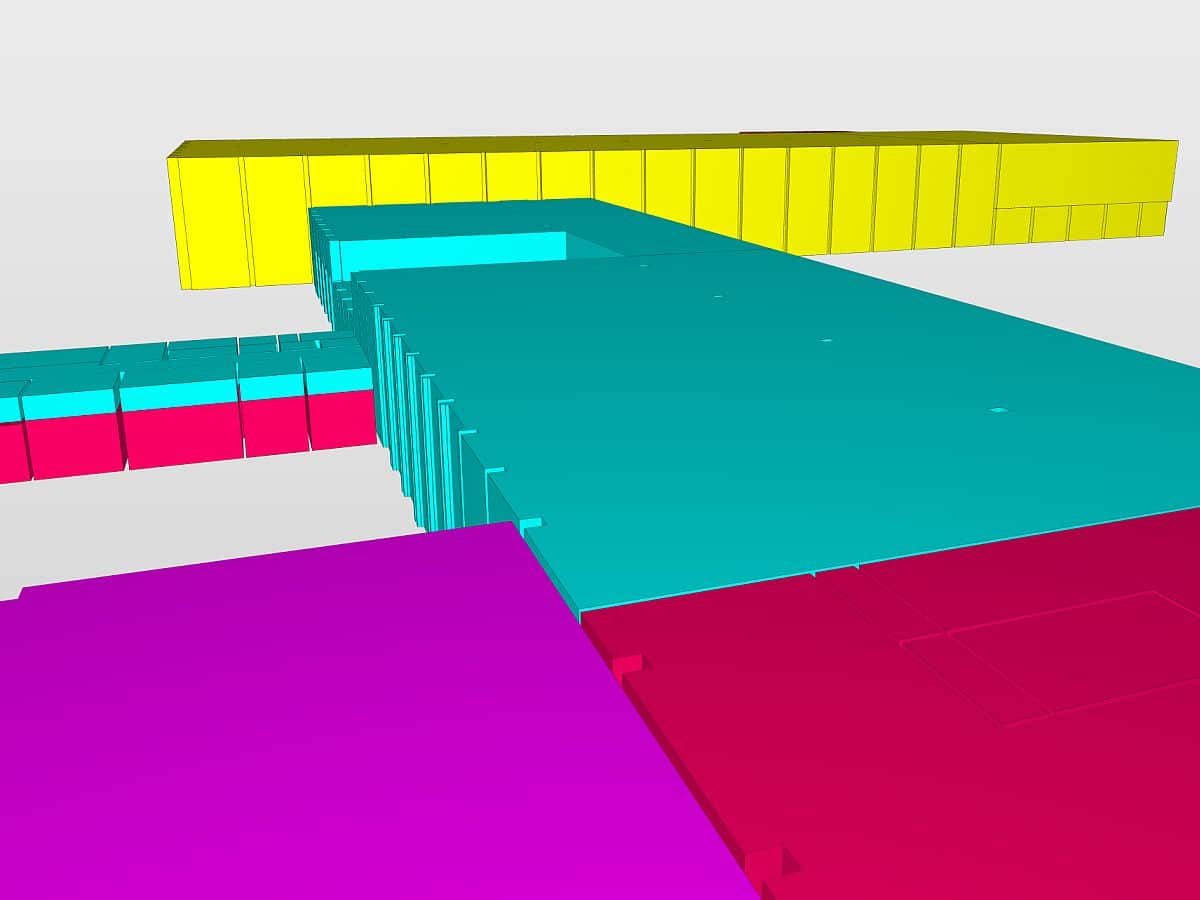
Extended modeling in LPH4
In general, a model detailing level of LOG 200 is sufficient in LPH4. Corresponding to the HOAI, components with the correct component dimensions can thus be represented in the model in a simplified manner, stating the item number, so that the "rough" space requirement of the shell construction can be recognized for further planning. For this project, the invitation to tender was planned after completion of LPH4, as the further execution, work and assembly planning was to be taken over by the general contractor. For this reason, a higher level of detail of LOG 300 was selected for the main components. It enables the bidders to recognize and correctly evaluate the more complex geometries.
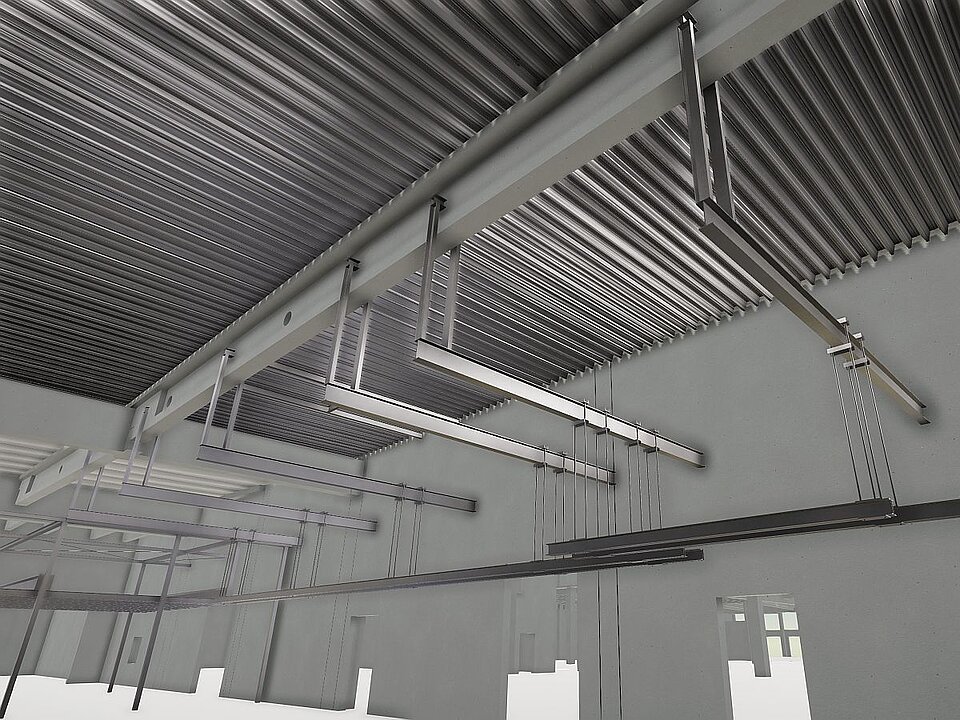
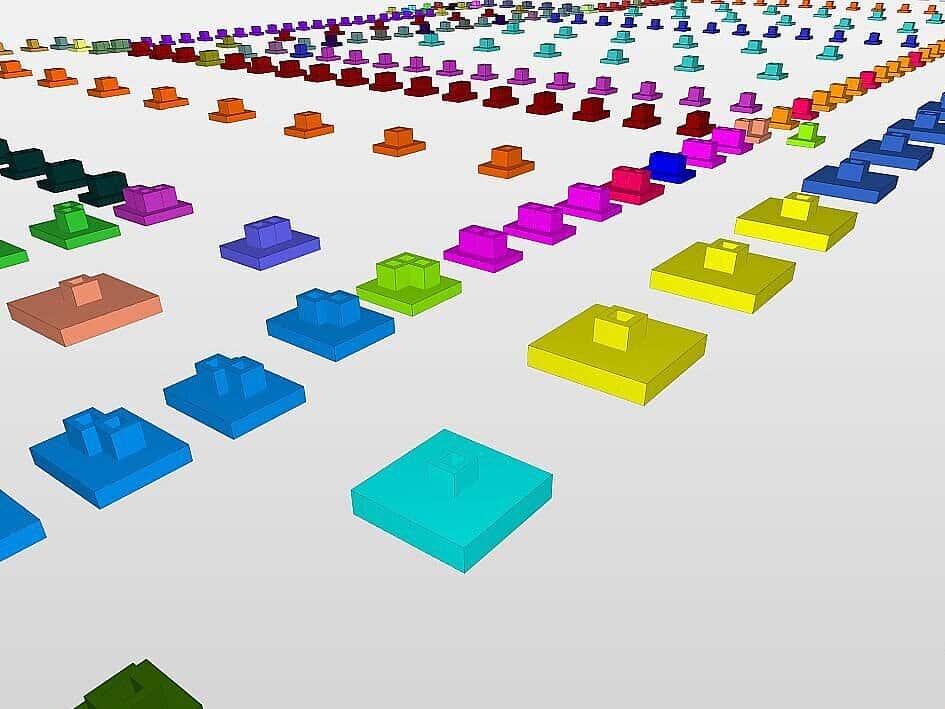
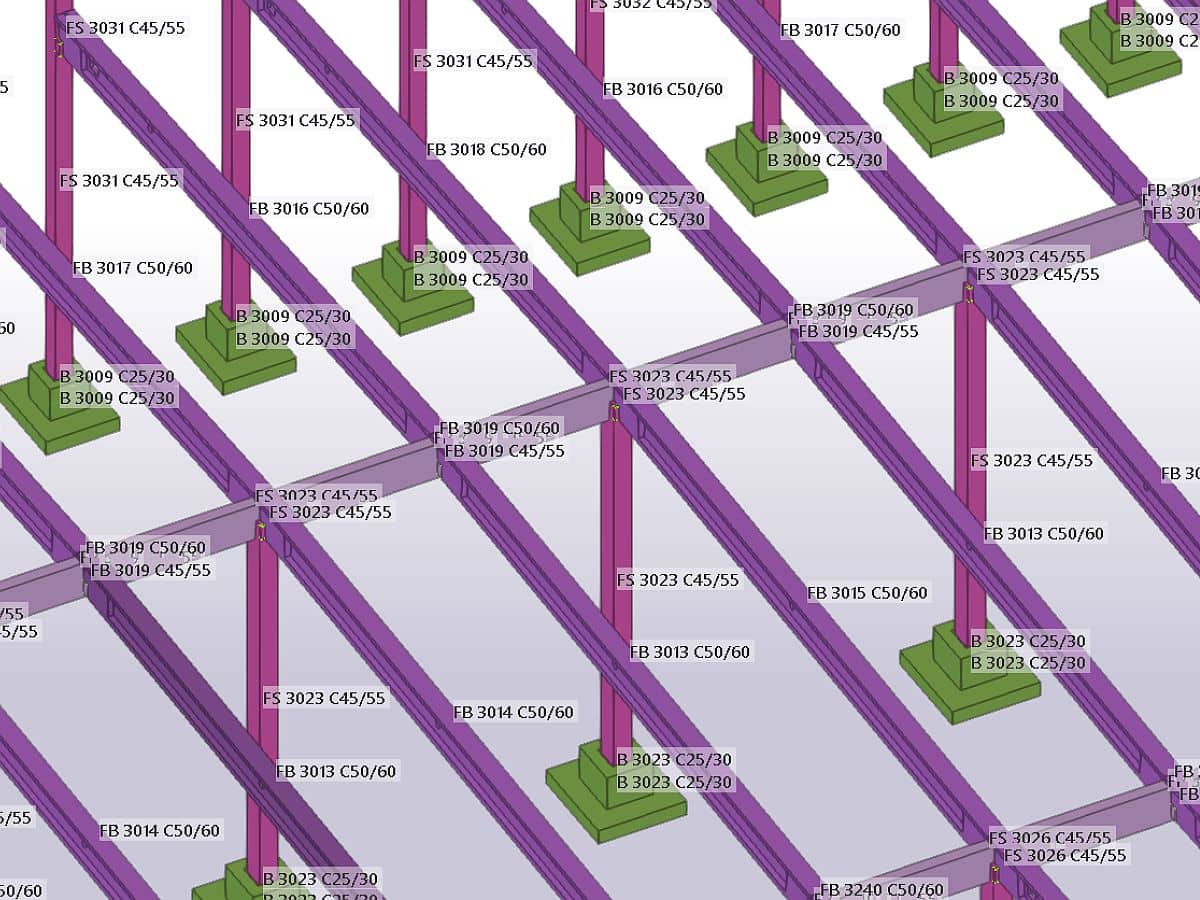
Construction progress control and invoicing
The challenge for construction progress control and invoicing is to record all the different information in the model - according to the respective use cases. To enable those responsible for construction progress control and invoicing to add their data to the planning model, we introduced a project platform that could be used to add further information to the planners' models. This platform does not require any additional software - the information can be entered directly online via input masks and the release and production status of the components can be visualized in colour. Once the assembly dates of the components have been entered into the model by the site manager, the proportion of the completed concrete quantities can be displayed immediately and evaluated for invoicing purposes.
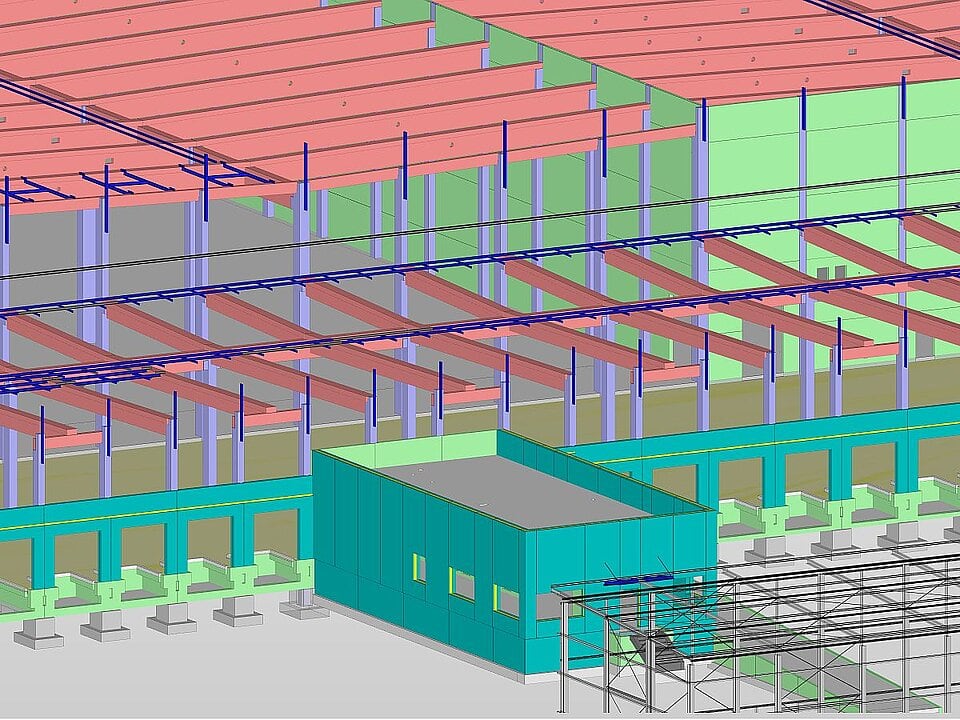